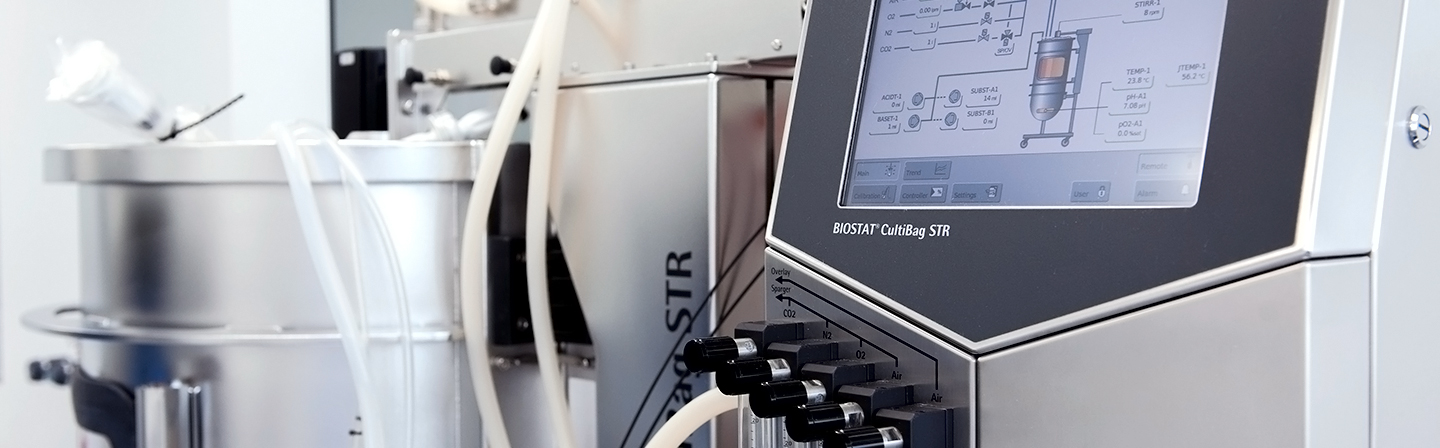
In recent years, the increasing number of biopharmaceuticals under preclinical and clinical development have required new flexible, efficient, and economic opportunities for GMP production of therapeutic antibody candidates. Small-scale batch production of test samples for late preclinical GLP animal studies or for phase-1 and phase-2 clinical studies is often not appropriate for large-scale manufacturing facilities in the industry. The Fraunhofer IZI, founded in 2005, investigates and develops solutions to such specific problems at the interfaces of medicine, life sciences and engineering.
The group has a completely qualified GMP antibody production facility. Our facility has a size of 180 m² and involves all clean room classes from D to A. The use of single-use equipment and materials enables an easy adaption to new process requirements. The GMP facility can be used for different contract manufacturing processes for preclinical and clinical (Phase 1/2) test samples as well as for process or instrument validation projects under consideration of special customer requests. The standard equipment can be easily broadened for new products.
In summary the main advantages are:
Future projects could include: